Prantsuse päikeseenergia instituut INES on välja töötanud uued PV -moodulid, mille termoplast ja looduslikud kiud on pärit Euroopas, näiteks lina ja basalt. Teadlaste eesmärk on vähendada päikesepaneelide keskkonnajalajälge ja kaalu, parandades samal ajal ringlussevõttu.
Taaskasutatud klaaspaneel esiküljel ja tagaküljel linane komposiit
Pilt: GD
Ajakirjast PV Prantsusmaalt
Prantsusmaa riikliku päikeseenergia instituudi (INES)-prantsuse alternatiivsete energiate ja aatomienergia komisjoni (CEA) osakonna teadlased-arendavad päikesemooduleid, millel on ees- ja tagakülgedel uusi biopõhiseid materjale.
"Kuna süsiniku jalajälg ja elutsükli analüüs on nüüd muutunud fotogalvaaniliste paneelide valimisel oluliseks kriteeriumiks, muutub materjalide hankimine järgneva paari aasta jooksul Euroopas oluliseks elemendiks," ütles CEA-Iinesi direktor Anis Fouini , intervjuus PV ajakirjale Prantsusmaale.
Uurimisprojekti koordinaator Aude Derrier ütles, et tema kolleegid on vaadanud mitmesuguseid juba olemasolevaid materjale, et leida selline, mis võimaldaks moodulite tootjatel toota paneele, mis parandavad jõudlust, vastupidavust ja kulusid, alandades samal ajal keskkonnamõju. Esimene meeleavaldaja koosneb heterojunktsioonidest (HTJ) päikesepatareidest, mis on integreeritud kogukomposiitmaterjali.
"Esikülg on valmistatud klaaskiust täidetud polümeerist, mis tagab läbipaistvuse," ütles Derrier. "Tagumine külg on valmistatud komposiidist, mis põhineb termoplastidel, milles on integreeritud kahe kiudude, lina ja basaltide kudumine, mis tagab mehaanilise tugevuse, kuid ka parema vastupidavuse õhuniiskusele."
Lina hangitakse Põhja -Prantsusmaalt, kus kogu tööstuslik ökosüsteem on juba olemas. Basalt hangitakse mujal Euroopas ja selle kootud INESi tööstuspartner. See vähendas süsiniku jalajälge 75 grammi süsinikdioksiidiga vatti, võrreldes sama võimsusega võrdlusmooduliga. Kaal oli ka optimeeritud ja see on alla 5 kilogrammi ruutmeetri kohta.
"See moodul on suunatud katusealusele PV -le ja hoonete integreerimisele," ütles Derrier. „Eeliseks on see, et see on loomulikult must värvusega, ilma et oleks vaja tagamaad. Ringlussevõtu osas on tänu termoplastidele, mida saab ümber mõelda, ka kihtide eraldamine tehniliselt lihtsam. ”
Moodulit saab teha ilma praeguseid protsesse kohandamata. Derrier ütles, et idee on tehnoloogia üle anda tootjatele ilma täiendavate investeeringuteta.
"Ainus hädavajalik on sügavkülmikute omamine materjali salvestamiseks, mitte vaigu ristsidumisprotsessi alustamiseks, kuid enamik tootjaid kasutab täna Prepregi ja on selleks juba varustatud," sõnas ta.
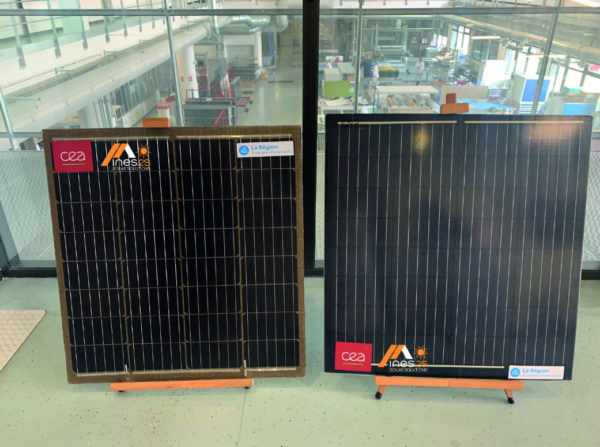
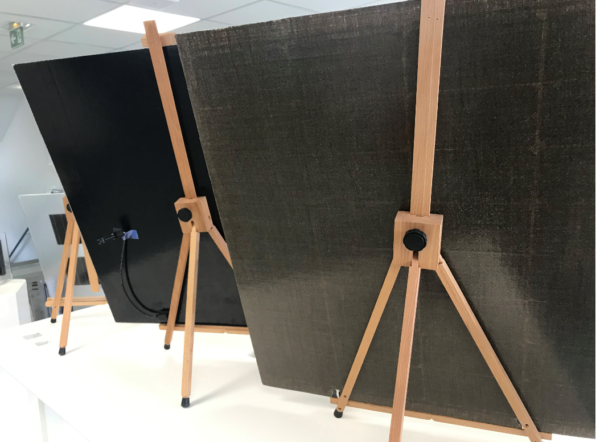
"Töötasime klaasi teise eluga ja töötasime välja mooduli, mis koosnes vanast moodulist pärinevast 2,8 mm klaasist," rääkis Derrier. "Oleme kasutanud ka termoplastilist kapselanti, mis ei vaja ristsidumist, mida on seetõttu lihtne taaskasutada, ja takistuse tagamiseks termoplastiline komposiit linakiuga."
Mooduli basaltivabal tagumisel pinnal on looduslik linavärv, mis võib näiteks fassaadi integreerimise osas olla esteetiliselt huvitav. Lisaks näitas INESi arvutusvahend süsiniku jalajälje vähenemist 10%.
"Nüüd on hädavajalik kahtluse alla seada fotogalvaanilised tarneahelad," ütles Jouini. „Rhône-Alpesi piirkonna abiga rahvusvahelise arenguplaani raames otsisime seetõttu mängijaid väljaspool päikeseenergia sektorit, et leida uusi termoplastid ja uusi kiude. Mõtlesime ka praeguse lamineerimisprotsessi üle, mis on väga energiamahukas. ”
Surve, pressimise ja jahutusfaasi vahel kestab lamineerimine tavaliselt 30–35 minutit, töötemperatuur on umbes 150 ° C kuni 160 C
"Kuid moodulite puhul, mis sisaldavad üha enam ökodisainitud materjale, on vaja muuta termoplastid umbes 200 ° C kuni 250 ° C, teades, et HTJ-tehnoloogia on kuumuse suhtes tundlik ja ei tohi ületada 200 c," ütles Derrier.
Uurimisinstituut teeb koostööd Prantsusmaal asuva induktsiooni termokompressioonispetsialisti Roctooliga, et vähendada tsükliaegu ja teha kujusid vastavalt klientide vajadustele. Üheskoos on nad välja töötanud mooduli, mille tagumine nägu on valmistatud polüpropüleenist tüüpi termoplastilisest komposiidist, millele on integreeritud ringlussevõetud süsinikkiud. Esikülg on valmistatud termoplastidest ja klaaskiust.
"Roctooli induktsiooni termokompressiooniprotsess võimaldab kahte esi- ja tagaplaati kiiresti soojendada, ilma et peaksite jõudma 200 ° C -ni HTJ rakkude tuumas," ütles Derrier.
Ettevõte väidab, et investeering on madalam ja protsess võib saavutada vaid mõne minuti tsükli aja, kasutades samal ajal vähem energiat. See tehnoloogia on suunatud komposiittootjatele, et anda neile võimalus toota erineva kuju ja suurusega osi, integreerides samal ajal kergemaid ja vastupidavamaid materjale.
Postiaeg: 24. juuni 201222